atelier Frontblenden Nachfertigung
- Sven Carstensen
- Eroberer
- Beiträge: 95
- Registriert: 12.01.2009, 16:40
- Wohnort: Worpswede
atelier Frontblenden Nachfertigung
Tach zusammen !
Ich habe jetzt ein Angebot zur Fertigung der Frontblendenprofile vorliegen.
Nachdem ich zunächst 250kg (!) mindestens abnehmen sollte, habe ich mich mit dem Hersteller auf eine Musterfertigung verständigt.
Der Meter "Atelierprofil" kostet demnach 1,90 Euro netto.
Allerdings fallen einmalig 1300 Euro Werkzeugkosten an.
Bei einer Abnahmemenge von 100 Blenden ergibt sich also ein Stückpreis von etwa 14 Euro, bei 50 Blenden von etwa 27 Euro usw...
Die Profile sind dann allerdings noch ungebohrt, was allerdings jeder Umbau-Interessierte leicht selbst bewerkstelligen dürfte.
Wie denkt Ihr darüber ? Wollen wir eine Sammelbestellung machen ??
Wie viele Umbauinteressierte gibt es hier noch und wieviele Geräte sind in (konkreter) Planung ?
Möchte vielleicht jemand gleich mehrere, gleiche Geräte bauen und diese dann am Markt anbieten ?
Freue mich auf Eure Rückmeldung !
Viele Grüße
Sven
Ich habe jetzt ein Angebot zur Fertigung der Frontblendenprofile vorliegen.
Nachdem ich zunächst 250kg (!) mindestens abnehmen sollte, habe ich mich mit dem Hersteller auf eine Musterfertigung verständigt.
Der Meter "Atelierprofil" kostet demnach 1,90 Euro netto.
Allerdings fallen einmalig 1300 Euro Werkzeugkosten an.
Bei einer Abnahmemenge von 100 Blenden ergibt sich also ein Stückpreis von etwa 14 Euro, bei 50 Blenden von etwa 27 Euro usw...
Die Profile sind dann allerdings noch ungebohrt, was allerdings jeder Umbau-Interessierte leicht selbst bewerkstelligen dürfte.
Wie denkt Ihr darüber ? Wollen wir eine Sammelbestellung machen ??
Wie viele Umbauinteressierte gibt es hier noch und wieviele Geräte sind in (konkreter) Planung ?
Möchte vielleicht jemand gleich mehrere, gleiche Geräte bauen und diese dann am Markt anbieten ?
Freue mich auf Eure Rückmeldung !
Viele Grüße
Sven
Ich bin Dabei!
Toller Einsatz Sven!
Hört sich erstmal erschreckend an, aber die Menge machts eben!
Ich nehme 5 Stück... und hoffe das es noch genug andere Interessenten gibt!
Sag bescheid, wenn´s soweit ist!
Gruß... Uli
Hört sich erstmal erschreckend an, aber die Menge machts eben!
Ich nehme 5 Stück... und hoffe das es noch genug andere Interessenten gibt!
Sag bescheid, wenn´s soweit ist!

Gruß... Uli
frontblenden-profil
also ich würde mir 2-3 'auf halde' legen wollen.
gruß
herbert

gruß
herbert
a2-af1-c4-cc4-cd5/2-dd4-gs3-lsv-ltv-m15-p4-pa4-rc1-rm7-rr1-st4²-sw2-tv3-vc4-vd4
atelier1-exporter-kh500-kh1000-l1-pc3-ps500-rt20-sk2-sk25-sk5-t1000cd-t22-t520-td1000-tg1000-tg1020-tgf3
atelier1-exporter-kh500-kh1000-l1-pc3-ps500-rt20-sk2-sk25-sk5-t1000cd-t22-t520-td1000-tg1000-tg1020-tgf3
- Sven Carstensen
- Eroberer
- Beiträge: 95
- Registriert: 12.01.2009, 16:40
- Wohnort: Worpswede
Hallo !
Ich habe jetzt erst mal das Strangpressprofil angefragt, die Unterschiede der Blenden kenne ich nicht im einzelnen. Ich glaube aber, dass der Querschnitt bei allen gleich ist ???? Vielleicht kann hier jemand eine Aufstellung machen ?
In nachfolgenden Arbeitsschritten müsste man dann noch ggf. fräsen/bohren.
Aber das muss ein Umbauinteressierter ja ohnehin.
Gruß Sven
Ich habe jetzt erst mal das Strangpressprofil angefragt, die Unterschiede der Blenden kenne ich nicht im einzelnen. Ich glaube aber, dass der Querschnitt bei allen gleich ist ???? Vielleicht kann hier jemand eine Aufstellung machen ?
In nachfolgenden Arbeitsschritten müsste man dann noch ggf. fräsen/bohren.
Aber das muss ein Umbauinteressierter ja ohnehin.
Gruß Sven
OK, es gibt meines Wissens 3 verschiedene Frontprofile:
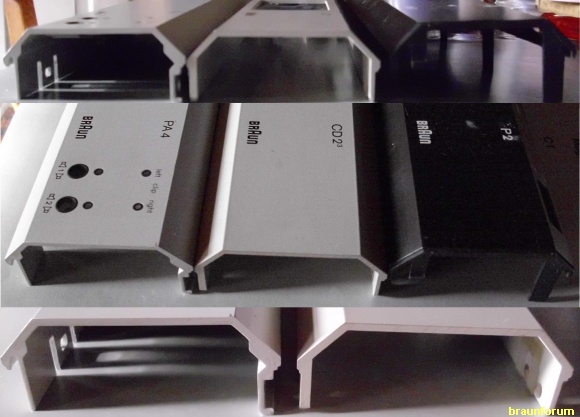
Typ1 links im Bild (Alu): T1, PA4, R4
Typ2 mitte im Bild (Alu): C1, C2, CD2³
Typ3 rechts im Bild (Plastik): P2, R1
Ich habe zwar noch andere Geräte, möchte diese aber erstmal nicht aufschrauben. Vielleicht könnt Ihr die Liste ja noch vervollständigen.
Typ 3 aus Plastik scheidet (meines erachtens) aus.... ist wirklich furchtbar daran ordendlich zu arbeiten, außerdem liegen die Werkzeugkosten für eine Plastiknachfertigung in etwa genauso hoch wie bei den Alufronten.
Andererseits wäre vielleicht die Mindestabnahmemenge geringer.
Typ1 hat viele Ecken und Kanten, dort wird der Werkzeugbauer das Fluchen anfangen und es wird durch den höheren Zeitaufwand sicher teurer als die Nachfertigung des Typ2´s.
Da wir ja die Chassis auch neu bauen wollen wären wir pracktisch auch Formunabhängig. Für Typ2 späche auch, das man Kasettengeräte sehr günstig aus der Bucht bekäme, wenn sich einer den Chassisnachbau ersparen möchte.
Nun ist Eure Meinung gefragt!
Gruß... Uli
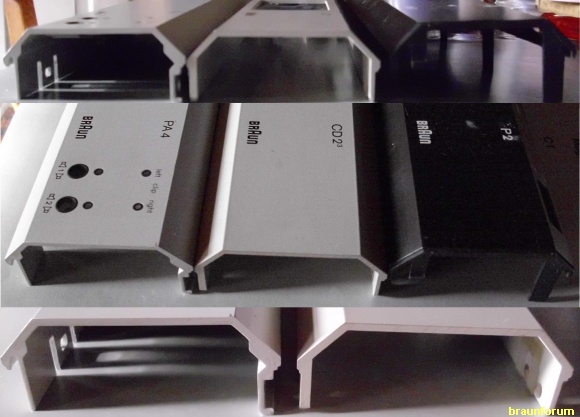
Typ1 links im Bild (Alu): T1, PA4, R4
Typ2 mitte im Bild (Alu): C1, C2, CD2³
Typ3 rechts im Bild (Plastik): P2, R1
Ich habe zwar noch andere Geräte, möchte diese aber erstmal nicht aufschrauben. Vielleicht könnt Ihr die Liste ja noch vervollständigen.
Typ 3 aus Plastik scheidet (meines erachtens) aus.... ist wirklich furchtbar daran ordendlich zu arbeiten, außerdem liegen die Werkzeugkosten für eine Plastiknachfertigung in etwa genauso hoch wie bei den Alufronten.
Andererseits wäre vielleicht die Mindestabnahmemenge geringer.
Typ1 hat viele Ecken und Kanten, dort wird der Werkzeugbauer das Fluchen anfangen und es wird durch den höheren Zeitaufwand sicher teurer als die Nachfertigung des Typ2´s.
Da wir ja die Chassis auch neu bauen wollen wären wir pracktisch auch Formunabhängig. Für Typ2 späche auch, das man Kasettengeräte sehr günstig aus der Bucht bekäme, wenn sich einer den Chassisnachbau ersparen möchte.
Nun ist Eure Meinung gefragt!
Gruß... Uli
Hallo,
die Zeichnung, die ich veröffentlicht habe, bezieht sich auf eine C1 Front.
Diese hat ein anderes Maß, als die CC4/R4 Fronten.
Die CD Blende hat innen lichte Höhe von:58,5mm
Die CC4 Blende hat innen lichte Höhe von: 54,5mm
Die A1 Blende hat innen lichte Höhe von: 54,0mm
Die CD Blende passt so ohne Weiteres nicht auf den T1 Rahmen drauf.
Am praktischsten wäre ein lichtes Maß der PA4, denn dann kann man diese Fronten auch dafür nehmen. Die PA4 Fronten sind sehr begehrt, da die neu nicht mehr bei Braunberni zu bekommen sind.
Das ganze bringt mich eigentlich wieder zu dem Schluss, dass es am besten ist, die Herstellung eines kompletten Leergehäuses.
Der Grundrahmen mit Rückwand ist ja sehr einfach herzustellen. Allerdings sind die beiden Seitenteile aus Kunststoff sicher auch nicht billig.
Ebenfalls besitzt der obere Deckel der Bausteine ja noch die vier Vertiefungen für die Füße weiterer Geräte.
Aber langfristig wird es sicher nicht genug "Schlachtgeräte" Geben und Braunberni hat ja auch nicht massenhaft Seitenteile ect.
Ich hätte also schon großes Interesse an kompletten Gehäusen.
Achja, ich würde mich mit 10 Frontblenden beteiligen.
Gruß
Gunnar
die Zeichnung, die ich veröffentlicht habe, bezieht sich auf eine C1 Front.
Diese hat ein anderes Maß, als die CC4/R4 Fronten.
Die CD Blende hat innen lichte Höhe von:58,5mm
Die CC4 Blende hat innen lichte Höhe von: 54,5mm
Die A1 Blende hat innen lichte Höhe von: 54,0mm
Die CD Blende passt so ohne Weiteres nicht auf den T1 Rahmen drauf.
Am praktischsten wäre ein lichtes Maß der PA4, denn dann kann man diese Fronten auch dafür nehmen. Die PA4 Fronten sind sehr begehrt, da die neu nicht mehr bei Braunberni zu bekommen sind.
Das ganze bringt mich eigentlich wieder zu dem Schluss, dass es am besten ist, die Herstellung eines kompletten Leergehäuses.
Der Grundrahmen mit Rückwand ist ja sehr einfach herzustellen. Allerdings sind die beiden Seitenteile aus Kunststoff sicher auch nicht billig.
Ebenfalls besitzt der obere Deckel der Bausteine ja noch die vier Vertiefungen für die Füße weiterer Geräte.
Aber langfristig wird es sicher nicht genug "Schlachtgeräte" Geben und Braunberni hat ja auch nicht massenhaft Seitenteile ect.
Ich hätte also schon großes Interesse an kompletten Gehäusen.
Achja, ich würde mich mit 10 Frontblenden beteiligen.
Gruß
Gunnar
Ich hoffe Ihr gebt mir Recht, wenn ich behaupte, das die Seitenteile alle auf jedes Chassis passen. Mir ist nur bekannt, das die letzten (senkrechte Schlitze) andere Befestigungsbohrungen haben. Bei einem Neubau müssten diese aber eh neu gebohrt werden.
BB hat aus der letzten Serie noch ein paar Neuteile, auch gebrauchte. Für 2 neue Graue habe ich 30 Euro pro Stück bezahlt. Aber aus Schlachtgeräten könnte ich noch mindestens 3 Geräte (6 Seiten) zusammen bekommen, diese sind eh schwarz und müssten gespachtelt & lackiert werden.
Ich tendiere auch zum Neubau des Chassis, welchen Fronttypen wir letzten Endes nehmen, ist mir eigendlich egal. Wenn ich ein Altgerät restaurieren wollte, würde ich die original verbaute Blende aufarbeiten.
Was hätte eine PA4 Front für Vorteile? Klar, sie ist geschlossen, aber wir bekommen komplett geschlossene Rohlinge ohne Löcher.
Ich bin immernoch für den Typ 2, da die Blende die größte lichte Höhe hat.
Gruß... Uli
BB hat aus der letzten Serie noch ein paar Neuteile, auch gebrauchte. Für 2 neue Graue habe ich 30 Euro pro Stück bezahlt. Aber aus Schlachtgeräten könnte ich noch mindestens 3 Geräte (6 Seiten) zusammen bekommen, diese sind eh schwarz und müssten gespachtelt & lackiert werden.
Ich tendiere auch zum Neubau des Chassis, welchen Fronttypen wir letzten Endes nehmen, ist mir eigendlich egal. Wenn ich ein Altgerät restaurieren wollte, würde ich die original verbaute Blende aufarbeiten.
Was hätte eine PA4 Front für Vorteile? Klar, sie ist geschlossen, aber wir bekommen komplett geschlossene Rohlinge ohne Löcher.
Ich bin immernoch für den Typ 2, da die Blende die größte lichte Höhe hat.
Gruß... Uli
Ich möchte mich Uli anschließen und halte auch Version 2 für die bessere Wahl.
Neben den vorgebrachten wichtigen Argumenten (Innenhöhe!) könnte die Blende m.E. trotzdem als PA4-Ersatz genutzt werden, indem man - z.B. mittels Alublech - die Innenhöhendifferenz ausgleichen kann.
Ich würde, auch um dieses tolle Projekt näher an die Realisierungsphase (benötigte Stückzahlen) zu bringen, ebenfalls 10 Frontblenden abnehmen.
Grüße
Christian
Neben den vorgebrachten wichtigen Argumenten (Innenhöhe!) könnte die Blende m.E. trotzdem als PA4-Ersatz genutzt werden, indem man - z.B. mittels Alublech - die Innenhöhendifferenz ausgleichen kann.
Ich würde, auch um dieses tolle Projekt näher an die Realisierungsphase (benötigte Stückzahlen) zu bringen, ebenfalls 10 Frontblenden abnehmen.
Grüße
Christian
Hallo und guten Tag,
ich halte die Version 1 für die bessere Wahl.
Das Argument, daß mit Version 2 4mm mehr Platz gewonnen wird, ist so nicht richtig, denn die 4mm fehlen nur im Bereich des Frontinnenrahmens.
Ich habe das Bild mal modifiziert und die Auflagefläche des Deckels mit eingezeichnet.
Ausserdem würden alle geschlitzten Bodenbleche, einschließlich des vom PA4 nicht passen, da die in die Nut in der Front eingelassen werden.
Ich würde 5 Stück abnehmen, aber wie gesagt, nur von Version 1.
Noch etwas. Die Befestigungslöcher der Kunststoffseitenwände sind bei geschlossenen und geschlitzten Versionen nicht gleich.

ich halte die Version 1 für die bessere Wahl.
Das Argument, daß mit Version 2 4mm mehr Platz gewonnen wird, ist so nicht richtig, denn die 4mm fehlen nur im Bereich des Frontinnenrahmens.
Ich habe das Bild mal modifiziert und die Auflagefläche des Deckels mit eingezeichnet.
Ausserdem würden alle geschlitzten Bodenbleche, einschließlich des vom PA4 nicht passen, da die in die Nut in der Front eingelassen werden.
Ich würde 5 Stück abnehmen, aber wie gesagt, nur von Version 1.
Noch etwas. Die Befestigungslöcher der Kunststoffseitenwände sind bei geschlossenen und geschlitzten Versionen nicht gleich.

Hallo und herzlich Willkommen im Forum ZZ Top!
Wenn man wirklich einen PA4 neu machen will, wäre es eh ratsam, ein neues Bodenblech mit mehr Luftschlitzen zu lasern. Die Front könnte mit Ausgleichsscheiben oder Blechstreifen der geringern Größe angepaßt werden. Aber ich gehe mal davon aus, das das ganze Chassis neu hergestellt wird, wo im entdefekt die Luft bzw. die Bef.Löcher gelasert werden bleibt einem dann selbst überlassen.
Bei den Plastik-Seitenteilen sind aber "nur" die Befestigungslöcher anders, diese müßte man aber eh in ein neues Chassis neu anbringen, da kann man dem Lasermann ja auch sagen, das er für beide Seitenausführung die Löcher macht damit man die Wahl hat, welche Seitenteile man montiert.
Bei den Blecharbeiten kann sich auch jeder Lokal einen Anbieter suchen, da diese Arbeiten nicht Stückzahlabhängig wären. Jedenfalls kann man dort schnell und unproblematisch die Maße ändern, wenn wir uns allerdings beim Alu einmal festgelegt haben gibts kein Zurück mehr!
Gruß... Uli
Wenn man wirklich einen PA4 neu machen will, wäre es eh ratsam, ein neues Bodenblech mit mehr Luftschlitzen zu lasern. Die Front könnte mit Ausgleichsscheiben oder Blechstreifen der geringern Größe angepaßt werden. Aber ich gehe mal davon aus, das das ganze Chassis neu hergestellt wird, wo im entdefekt die Luft bzw. die Bef.Löcher gelasert werden bleibt einem dann selbst überlassen.
Bei den Plastik-Seitenteilen sind aber "nur" die Befestigungslöcher anders, diese müßte man aber eh in ein neues Chassis neu anbringen, da kann man dem Lasermann ja auch sagen, das er für beide Seitenausführung die Löcher macht damit man die Wahl hat, welche Seitenteile man montiert.
Bei den Blecharbeiten kann sich auch jeder Lokal einen Anbieter suchen, da diese Arbeiten nicht Stückzahlabhängig wären. Jedenfalls kann man dort schnell und unproblematisch die Maße ändern, wenn wir uns allerdings beim Alu einmal festgelegt haben gibts kein Zurück mehr!
Gruß... Uli
Hallo, mein Projekt ist der Bau eines Media-PCs und da ist es eigentlich egal welches Profil benutzt wird. Besser wäre es ein gesamtes Gehäuse zu haben, denn es tut einfach weh ein Braun-Gerät (welches auch immer) zu schlachten. Also mit 3 Teilen wäre ich dabei - egal welches Profil - aber wenn es der Wahrheitsfindung dient - PA4 wäre wohl etwas besser für mein Projekt...
Guten Rutsch an alle und bitte weiter so..
QV
Guten Rutsch an alle und bitte weiter so..
QV
neue Fronten... gestorben ¿
Hallo QV,
herzlich Willkommen bei uns!
Leider ist das Projekt wohl gestorben, da keiner die Zeit hat oder den finaziellen Teil stemmen möchte (ca.1500-2000€ für den Formenbauer) oder einen geeigneten Prototypen-Bauer kennt. Alle schreckt natürlich auch der Preis ab, hier kommen schnell (je nach Auflage) 100-200 € pro Front zusammen.
Bei den Blech-Gehäuseteilen sähe es da anders aus, schon ab einer Auflage von 5 Stück wäre ein Preis von ca.20 € pro Blechteil (gelasert & gekantet) möglich.
Allen hier einen guten Rutsch ins neue Jahr!!
Gruß.... Uli
herzlich Willkommen bei uns!
Leider ist das Projekt wohl gestorben, da keiner die Zeit hat oder den finaziellen Teil stemmen möchte (ca.1500-2000€ für den Formenbauer) oder einen geeigneten Prototypen-Bauer kennt. Alle schreckt natürlich auch der Preis ab, hier kommen schnell (je nach Auflage) 100-200 € pro Front zusammen.
Bei den Blech-Gehäuseteilen sähe es da anders aus, schon ab einer Auflage von 5 Stück wäre ein Preis von ca.20 € pro Blechteil (gelasert & gekantet) möglich.
Allen hier einen guten Rutsch ins neue Jahr!!
Gruß.... Uli
Fronten aus Plastik?
Hallo Forum,
da ja anscheinend der Alu-Fronten Nachbau aus Kostengründen scheitert, was sehr schade ist, wäre vielleicht eine alternative Plastik.
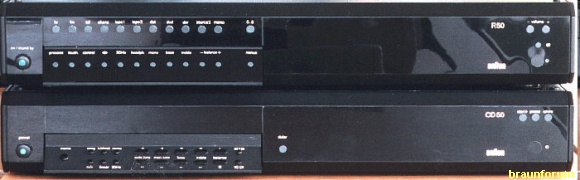
Hier ein Bild der Nachfolger, auch hier wurden die Fronten aus Plastik oder Acryl gefertigt. Der Vorteil wären die fehlenden Display Fenster bei schwarzen Anlagen. Auch die leichtere Bearbeitung wäre von Vorteil.
Leider kenne ich keinen der "in Plastik" macht... Ihr?
Gruß.. Uli
da ja anscheinend der Alu-Fronten Nachbau aus Kostengründen scheitert, was sehr schade ist, wäre vielleicht eine alternative Plastik.
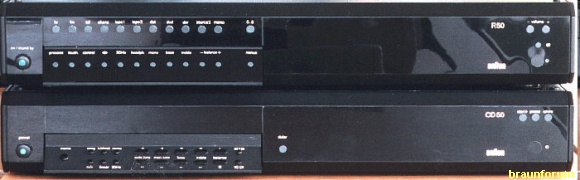
Hier ein Bild der Nachfolger, auch hier wurden die Fronten aus Plastik oder Acryl gefertigt. Der Vorteil wären die fehlenden Display Fenster bei schwarzen Anlagen. Auch die leichtere Bearbeitung wäre von Vorteil.
Leider kenne ich keinen der "in Plastik" macht... Ihr?
Gruß.. Uli
Re: Fronten aus Plastik?
also ehrlichUli hat geschrieben:.... wäre vielleicht eine alternative Plastik.

Gunnar
- Paparierer
- Moderator
- Beiträge: 2759
- Registriert: 28.12.2010, 15:36
- Wohnort: 85077 Manching
So: Freies Schußfeld für Diskussion
Liebe Eigen-/Umbauwillige,
Ihr habt Euch sehr intensiv mit dem Front-Thema beschäftigt und seid (fast*) immer davon ausgegangen, dass die Fronten aus einem Strangprofil entstehen sollten, was ein teures Werkzeug voraussetzt.
(*Ausnahme: Der Vorschlag, die Front aus dem Vollem oder einem starken U fräsen)
Da ich ja noch recht frisch und grün hier bin, habe ich von einer anderen Seite hingeschaut und billigere Fertigungsverfahren gesucht und darf ungestraft rumspinnen...
Eingefallen sind mir Kanten/Biegen bzw. das Zusammenfügen einzelner Teilstücke.
Beim Kanten sind natürlich die Radien an den Biegestellen das Problem, da man dort nicht die schön definierte "spitze" Kante erhält, sondern einen Biegeradius von ca. 2x Materialdicke (innen) und ca. 3x Materialdicke (außen). vom Radius senkrecht bis zur Kante sind es dann ca. 0,5mm - das sieht man halt. Da ist dann die Frage, ob sich das mit Modellbauspachtel o.ä. für unsre ästhetischen Ansprüche ausreichend gut modellieren lässt.
Für das Zusammenfügen käme Kleben oder Löten in Frage (Schweißen benötigt zu viel Hitze). Da die mechanische Belastung bei der Bedienung der Anlage eher gering ist, plädiere ich für Kleben. Beim Löten ist es auch eine Frage der Genauigkeit, und die Werkstücke müssten auch stark erhitzt werden; zudem gibt es Probleme mit der Oxidschicht (<- Näheres bitte im Netz lesen, da bin ich nicht so firm - Werkstoffkunde war mir immer ein Greuel!).
Soviel vorneweg. Nun zu den Skizzen. Ausgegangen bin ich von Gunnars (Danke!) Zeichnung, herausgekommen sind vier Varianten, die in der angehängten Datei von der Seite aus gesehen "skizziert" sind. Die "Laschen" dienen zum Verschrauben der Blende mit dem Chassis.
Nun von rechts nach links:
1. Gekantetes Profil mit angeklebten Laschen jeweils gleicher Dicke. Unten, wo ein Millimeter mehr gebraucht wird, ist einfach noch ein Streifen geeigneter Dicke "draufgepappt". An den Ecken des U hat die Schattenfuge zum Deckel- bzw. Bodenblech dann eher eine V- als eine Kastenform. (Finde ich nicht so schlimm.) Die obere und die untere Kante des U-Blechs müßte im 45°Winkel gebrochen werden. Um die Teile sauber miteinander zu verkleben, müsste eine Lehre verwendet werden.
2. Front aus Einzelteilen. Die Stöße, wo die einzelnen Streifen verklebt werden, sollten meiner Ansicht nach genau bei den Kanten liegen. Die Laschen sind exakt gleich und können gefräst werden (- denke ich im nicht mehr jugendlichen Überschwang).
3. Kombination aus 1. und 2. (=Mein Favorit)
4. Aufwändigere Kombination aus 1. und 2.
So, und nun: Feuer frei für Eure Gedanken!
Beste Grüße, Gereon
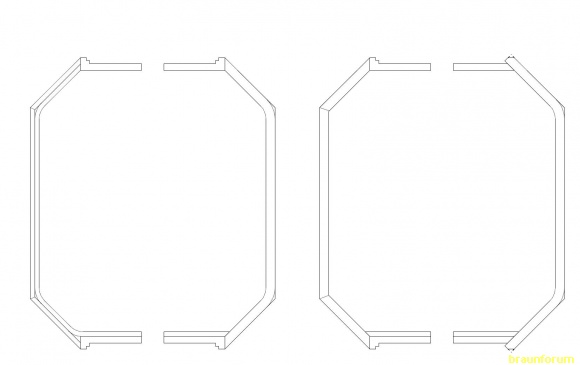
by the way: Ich könnte durchaus eine 3D-Datei in 1:1 im Microstation (dgn) oder AutoCad (dxf oder dwg) - Format erstellen, falls diese benötigt wird.
Ihr habt Euch sehr intensiv mit dem Front-Thema beschäftigt und seid (fast*) immer davon ausgegangen, dass die Fronten aus einem Strangprofil entstehen sollten, was ein teures Werkzeug voraussetzt.
(*Ausnahme: Der Vorschlag, die Front aus dem Vollem oder einem starken U fräsen)
Da ich ja noch recht frisch und grün hier bin, habe ich von einer anderen Seite hingeschaut und billigere Fertigungsverfahren gesucht und darf ungestraft rumspinnen...


Eingefallen sind mir Kanten/Biegen bzw. das Zusammenfügen einzelner Teilstücke.
Beim Kanten sind natürlich die Radien an den Biegestellen das Problem, da man dort nicht die schön definierte "spitze" Kante erhält, sondern einen Biegeradius von ca. 2x Materialdicke (innen) und ca. 3x Materialdicke (außen). vom Radius senkrecht bis zur Kante sind es dann ca. 0,5mm - das sieht man halt. Da ist dann die Frage, ob sich das mit Modellbauspachtel o.ä. für unsre ästhetischen Ansprüche ausreichend gut modellieren lässt.
Für das Zusammenfügen käme Kleben oder Löten in Frage (Schweißen benötigt zu viel Hitze). Da die mechanische Belastung bei der Bedienung der Anlage eher gering ist, plädiere ich für Kleben. Beim Löten ist es auch eine Frage der Genauigkeit, und die Werkstücke müssten auch stark erhitzt werden; zudem gibt es Probleme mit der Oxidschicht (<- Näheres bitte im Netz lesen, da bin ich nicht so firm - Werkstoffkunde war mir immer ein Greuel!).
Soviel vorneweg. Nun zu den Skizzen. Ausgegangen bin ich von Gunnars (Danke!) Zeichnung, herausgekommen sind vier Varianten, die in der angehängten Datei von der Seite aus gesehen "skizziert" sind. Die "Laschen" dienen zum Verschrauben der Blende mit dem Chassis.
Nun von rechts nach links:
1. Gekantetes Profil mit angeklebten Laschen jeweils gleicher Dicke. Unten, wo ein Millimeter mehr gebraucht wird, ist einfach noch ein Streifen geeigneter Dicke "draufgepappt". An den Ecken des U hat die Schattenfuge zum Deckel- bzw. Bodenblech dann eher eine V- als eine Kastenform. (Finde ich nicht so schlimm.) Die obere und die untere Kante des U-Blechs müßte im 45°Winkel gebrochen werden. Um die Teile sauber miteinander zu verkleben, müsste eine Lehre verwendet werden.
2. Front aus Einzelteilen. Die Stöße, wo die einzelnen Streifen verklebt werden, sollten meiner Ansicht nach genau bei den Kanten liegen. Die Laschen sind exakt gleich und können gefräst werden (- denke ich im nicht mehr jugendlichen Überschwang).
3. Kombination aus 1. und 2. (=Mein Favorit)
4. Aufwändigere Kombination aus 1. und 2.
So, und nun: Feuer frei für Eure Gedanken!
Beste Grüße, Gereon
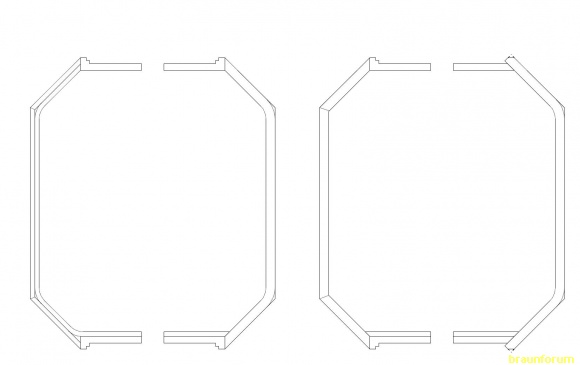
by the way: Ich könnte durchaus eine 3D-Datei in 1:1 im Microstation (dgn) oder AutoCad (dxf oder dwg) - Format erstellen, falls diese benötigt wird.
- Paparierer
- Moderator
- Beiträge: 2759
- Registriert: 28.12.2010, 15:36
- Wohnort: 85077 Manching
einen Schritt weiter
Vorstellbar wäre auch, ein Alublech von 2,5mm Dicke zu kanten und danach 0,5mm herunterzufräsen. Damit erhält man dann die gewohnte Kante. Wie gut 2,5mm-Blech zu kanten ist, weiss ich allerdings nicht. Die Abkantbänke "für den Hausgebrauch" lassen solch eine Materialdicke nicht zu.
In der nachfolgenden Datei ist daher neben der Version (rechts) mit 2,5mm Stärke auch (links) eine mit 2mm Stärke dargestellt, bei der ebenfalls heruntergefräst werden muss. Damit wäre die Frontseite nur noch 1,5mm stark, aber das sollte doch eigentlich kein Problem darstellen, oder?

noch keine Antwort... ...no discussion available
Schönes Wochenende wünscht
Gereon
In der nachfolgenden Datei ist daher neben der Version (rechts) mit 2,5mm Stärke auch (links) eine mit 2mm Stärke dargestellt, bei der ebenfalls heruntergefräst werden muss. Damit wäre die Frontseite nur noch 1,5mm stark, aber das sollte doch eigentlich kein Problem darstellen, oder?



Schönes Wochenende wünscht
Gereon
Hi Gereon!
im Prinzip ist alles machbar, für eine Kleinserie bestimmt auch bezahlbar.
Wenn ich es richtig verstanden habe würdest Du die einzelnen Bleche vorfräsen und dann zusammenkleben. Da die 45° Schräge aber nur ca.14mm hat, müssten (um eine saubere Kante zu bekommen) diese 14 mm auch eine 45° Schräge haben, so wie jeweils in den linken Bildern zu sehen ist. Bei der Länge der Front frage ich mich, wie Du diesen Streifen einspannen willst um eine saubere Kante anzufräsen.... geht das?
Aus meiner Erfahrung beim Bund (ich arbeitete im Flugzeugbau) weis ich noch, das Alubleche zum kanten vorher weichgeglüht und abgeschreckt wurden, dieses machte für eine gewisse Zeit das Alu weich und biegsam, so das es nicht an den Kantungen reißt. Dieses ist sehr viel Aufwand... da bin ich gespannt ob Du auch eine 4ma in der Hinterhand hast, die solche Kantungen bewerkstelligen kann.
Ich bin aber guter Dinge und lasse mich gerne eines besseren belehren.... will sagen: ich würde auch Fronten abnehmen, wenn es gelingt die zu einem Preis von 50€/Stück herzustellen. Alles teurere würde (m.E.) den Aufwand nicht lohnen, da man dann auch andere Geräte schlachten könnte.
Ich denke, wenn Du es wirklich fäsen lassen willst, sind da viele Aufspannungen nötig, da Du viele filigrane Kanten hast:
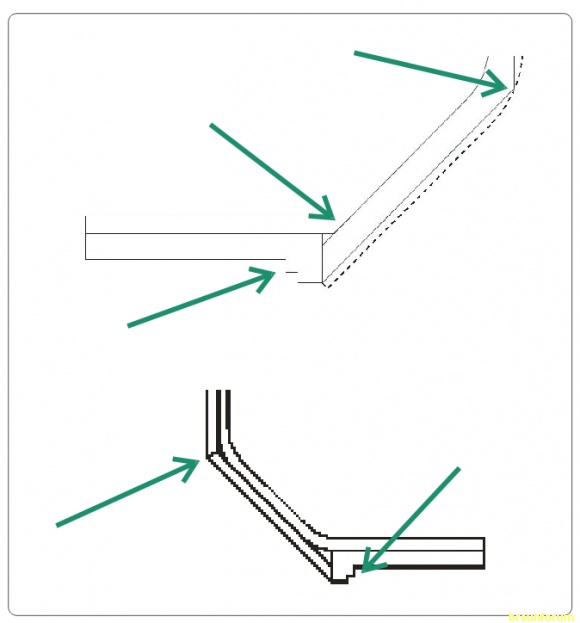
Vielleicht müssen diese Kanten garnicht sein und dadurch würde die Front günstiger in der Herstellung!?
Gruß... Uli
im Prinzip ist alles machbar, für eine Kleinserie bestimmt auch bezahlbar.
Wenn ich es richtig verstanden habe würdest Du die einzelnen Bleche vorfräsen und dann zusammenkleben. Da die 45° Schräge aber nur ca.14mm hat, müssten (um eine saubere Kante zu bekommen) diese 14 mm auch eine 45° Schräge haben, so wie jeweils in den linken Bildern zu sehen ist. Bei der Länge der Front frage ich mich, wie Du diesen Streifen einspannen willst um eine saubere Kante anzufräsen.... geht das?
Aus meiner Erfahrung beim Bund (ich arbeitete im Flugzeugbau) weis ich noch, das Alubleche zum kanten vorher weichgeglüht und abgeschreckt wurden, dieses machte für eine gewisse Zeit das Alu weich und biegsam, so das es nicht an den Kantungen reißt. Dieses ist sehr viel Aufwand... da bin ich gespannt ob Du auch eine 4ma in der Hinterhand hast, die solche Kantungen bewerkstelligen kann.
Ich bin aber guter Dinge und lasse mich gerne eines besseren belehren.... will sagen: ich würde auch Fronten abnehmen, wenn es gelingt die zu einem Preis von 50€/Stück herzustellen. Alles teurere würde (m.E.) den Aufwand nicht lohnen, da man dann auch andere Geräte schlachten könnte.
Ich denke, wenn Du es wirklich fäsen lassen willst, sind da viele Aufspannungen nötig, da Du viele filigrane Kanten hast:
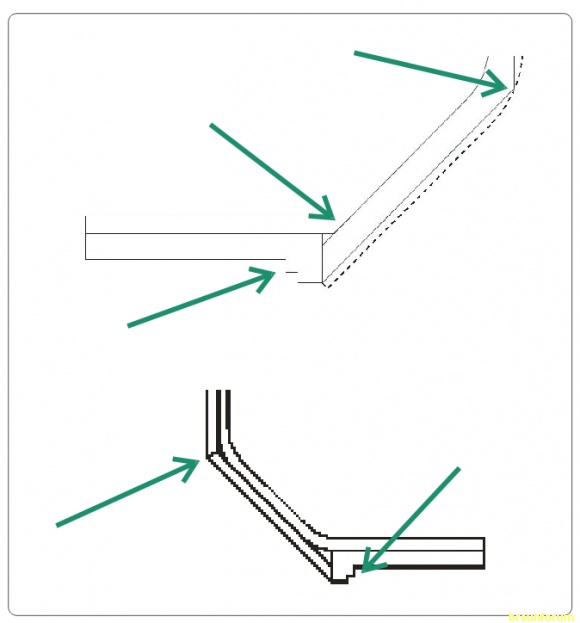
Vielleicht müssen diese Kanten garnicht sein und dadurch würde die Front günstiger in der Herstellung!?
Gruß... Uli
- Paparierer
- Moderator
- Beiträge: 2759
- Registriert: 28.12.2010, 15:36
- Wohnort: 85077 Manching
Das mit dem Vorfräsen wäre für die 14mm-Stücke (falls man diese Variante nehmen will) etwa so: Da nimmt man dann einen 30mm Streifen, fräst mittig eine zweistufige Nut aus und sägt ihn dann (2mm Sägeblatt) in der Mitte entlang durch und erhält einen Streifen für oben und einen für unten. Bei der anderen Variante würde ich genauso einen Streifen von 2x45mm plus sqr(2) x Sägeblattdicke nehmen und unter 45°Winkel der Länge nach durch die Säge schieben.Uli hat geschrieben: Wenn ich es richtig verstanden habe würdest Du die einzelnen Bleche vorfräsen und dann zusammenkleben.
Der gekantete Stirnteil müsste ebenfalls vorher die 45° Schrägen bekommen (45° schräg der Länge nach sägen?). Dann wird er gekantet, dann 3x eingespannt und den Biegeradius runtergefräst. Damit man die Teile besser einspannen kann, würde ich sie erst nachher auf die 43,5cm ablängen. Ist das verständlich? Manchmal verstehe ich mich selbst nicht...
Deswegen habe ich die andere Variante, bei der nur die Längskante des Stirnblechs unter 45° "gebrochen" wird. Der ganze Rest geht dann (theoretisch!) mit 2x Kanten und 3x fräsen.Uli hat geschrieben: Ich denke, wenn Du es wirklich fäsen lassen willst, sind da viele Aufspannungen nötig, da Du viele filigrane Kanten hast:
Vielleicht müssen diese Kanten garnicht sein und dadurch würde die Front günstiger in der Herstellung!?
Ich schau mal in der nächsten Zeit, ob ich jemanden in unserem Werkzeugbau oder dem Bildungszentrum für die Problemstellung interessieren kann.
Beste Grüße, Gereon
Das wäre sicher theoretisch möglich, aber bedenke... es ist Alu.
Mit Holz ist das eine gängige Praxis, Gehrungen werden so hergestellt.
Das Problem beim Aluschneiden: es franzt aus und Du hast bei 45° einen großen Grad an den Schnittkanten. Ich denke das wird so nicht klappen.
Alu erodieren wäre eine Möglichkeit... ist aber sündhaft teuer
!
Gruß... Uli
Mit Holz ist das eine gängige Praxis, Gehrungen werden so hergestellt.
Das Problem beim Aluschneiden: es franzt aus und Du hast bei 45° einen großen Grad an den Schnittkanten. Ich denke das wird so nicht klappen.
Alu erodieren wäre eine Möglichkeit... ist aber sündhaft teuer

Gruß... Uli
- Paparierer
- Moderator
- Beiträge: 2759
- Registriert: 28.12.2010, 15:36
- Wohnort: 85077 Manching
Nochmals Danke für die Hinweise, ich werde die ganzen Aspekte mal mit meinen Bekannten im Werkzeugbau diskutieren und Euch dann weitergeben, was dabei herausgekommen ist.Uli hat geschrieben:Das wäre sicher theoretisch möglich, aber bedenke... es ist Alu.
Mit Holz ist das eine gängige Praxis, Gehrungen werden so hergestellt.
Das Problem beim Aluschneiden: es franzt aus und Du hast bei 45° einen großen Grad an den Schnittkanten. Ich denke das wird so nicht klappen.
Alu erodieren wäre eine Möglichkeit... ist aber sündhaft teuer!
Gruß... Uli
Gruß, Gereon
- Paparierer
- Moderator
- Beiträge: 2759
- Registriert: 28.12.2010, 15:36
- Wohnort: 85077 Manching
Nach einer Diskussion mit einem Werkzeugbauer...
...gibt es diese Ergebnis:
Das Kanten bringt man bei den Dimensionen nicht gescheit (=genau genug) hin.
Zusammenstückeln aus fünf Teilen wird wahrscheinlich zu instabil.
Die Frage ist aber, ob man die Frontplatte und die ca. 12mmx12mm-45°-Schräge in einem Stück als Profil nicht wesentlich billiger bekommen kann als das Komplett-Teil.

Wer hat einen Alu-Strang-Press-Profil-Werkzeug-Bauer in der Bekanntschaft, der dazu etwas sagen kann?
Gruß, Gereon
Das Kanten bringt man bei den Dimensionen nicht gescheit (=genau genug) hin.
Zusammenstückeln aus fünf Teilen wird wahrscheinlich zu instabil.
Die Frage ist aber, ob man die Frontplatte und die ca. 12mmx12mm-45°-Schräge in einem Stück als Profil nicht wesentlich billiger bekommen kann als das Komplett-Teil.

Wer hat einen Alu-Strang-Press-Profil-Werkzeug-Bauer in der Bekanntschaft, der dazu etwas sagen kann?
Gruß, Gereon
_______________________________
meistens ist es was mechanisches...
_______________________________
„Audiophile verwenden ihre Geräte nicht, um Ihre Musik zu hören.
Audiophile verwenden Ihre Musik, um ihre Geräte zu hören.“
Alan Parsons
meistens ist es was mechanisches...
_______________________________
„Audiophile verwenden ihre Geräte nicht, um Ihre Musik zu hören.
Audiophile verwenden Ihre Musik, um ihre Geräte zu hören.“
Alan Parsons
- Sven Carstensen
- Eroberer
- Beiträge: 95
- Registriert: 12.01.2009, 16:40
- Wohnort: Worpswede
... womit sich der Kreis geschlossen hätte und wir bei meinem ersten Posting dieses threads wären. Ich habe diese Profile doch seinerzeit angefragt ! (bitte lesen)
Es scheiterte einzig und allein an der Stückzahl und der Vorleistung.
Wenn jemand hier bereit wäre die Werkzeugkosten auszulegen, ist die Herstellung kein Problem.
Grüße
Sven
Es scheiterte einzig und allein an der Stückzahl und der Vorleistung.
Wenn jemand hier bereit wäre die Werkzeugkosten auszulegen, ist die Herstellung kein Problem.
Grüße
Sven